Everything is connected
Digitalisation, artificial intelligence and robotics: technology mega trends are driving huge disruption to the world of manufacturing across the planet. Humans, machines and processes are becoming ever more closely interwoven as we strive to improve productivity. In many cases, physically strenuous work is being eliminated for employees and replaced by other tasks requiring expertise in this evermore - complex production environment. Nobody knows exactly where we are heading – but the journey is certainly an exciting one!
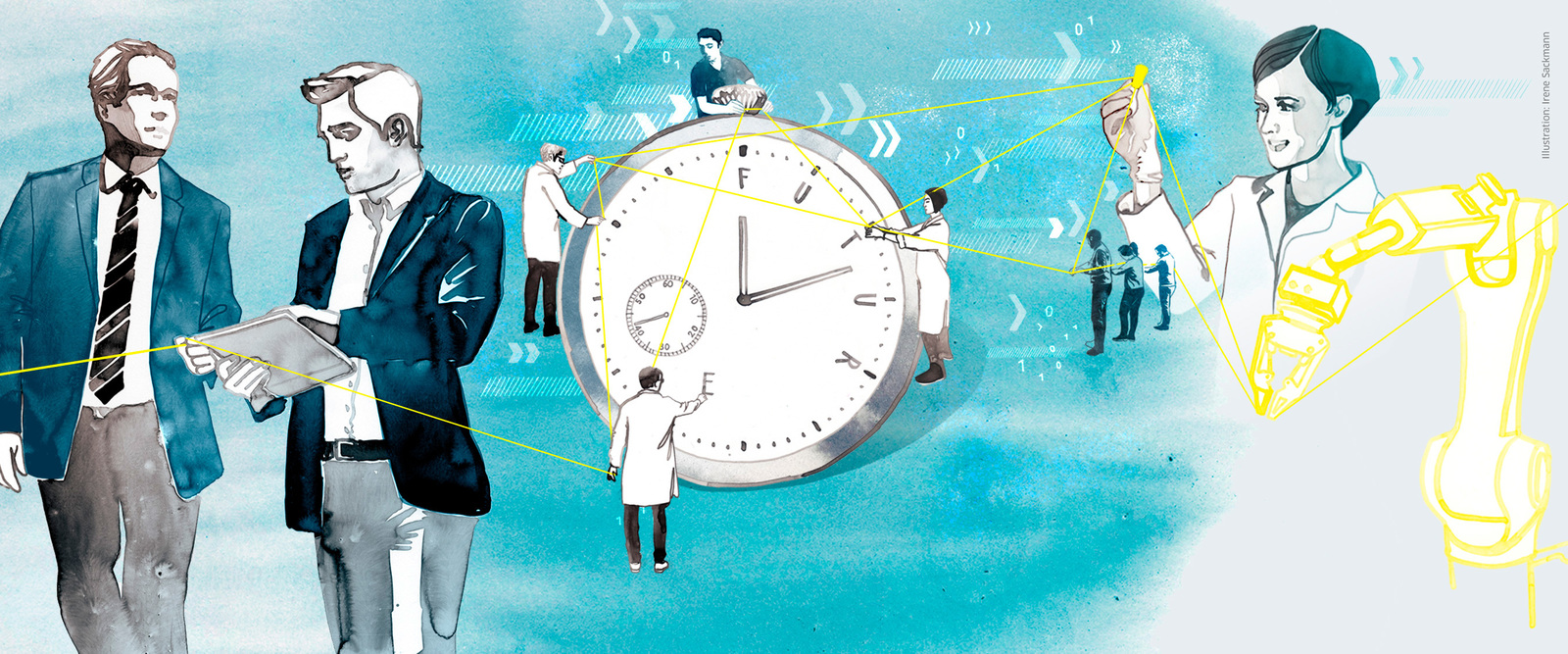
A tangible future
For example, in Bühlertal
Manufacturing locally while remaining competitive. Implementing client requests in high quality at high speed. Assuring the longterm existence and sustainability of our site. Kärcher is heading in this direction and going fully digital at the Bühlertal site. Even before the Bühlertal 5.0 project started, the plant was already over 50 % automated. Within just two years, production control, manufacturing and intralogistics had all been introduced or further automated. But why do driverless vehicles need swarm intelligence and why do employees now have to carry much less weight? Let’s take a look.
Taking seasonal work digital: business goes on
Large projects have a habit of petering out before they come to anything. This is a particular problem when the scope is too big and employees are not on board. Katja Räntzsch, project manager for Bühlertal 5.0, explains: “Right from the start, it was important that all staff were involved because they are the ones who will have to take on many of the tasks in the implementation process. That can only happen if they are motivated and open to new ideas – not to mention that business goes on and we have to reliably run the operational side of things, too.”
In Bühlertal, operations comprise, for example, in-house plastic manufacturing of 50,000 components every day and the production of 25,000 products for domestic and professional use. Then there is the particular challenge posed by cleaning technology being a seasonal business. In the retail segment, demand for high-pressure cleaners is especially high in spring and summer. “As soon as the sun comes out, orders spike and they need fulfilling quickly – so we work with a team of 570 permanent staff plus an additional 300 seasonal staff across three shifts,” explains Räntzsch.
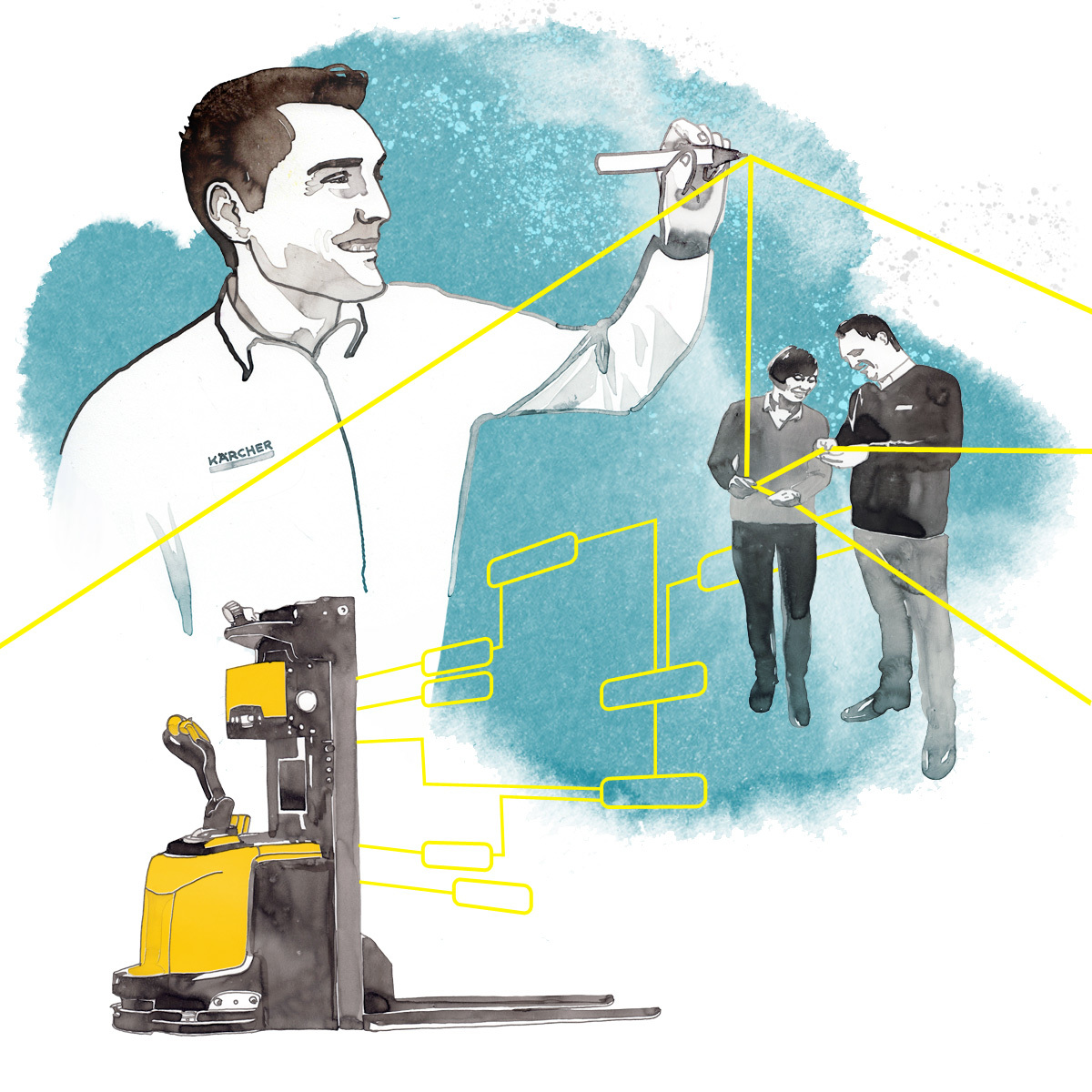
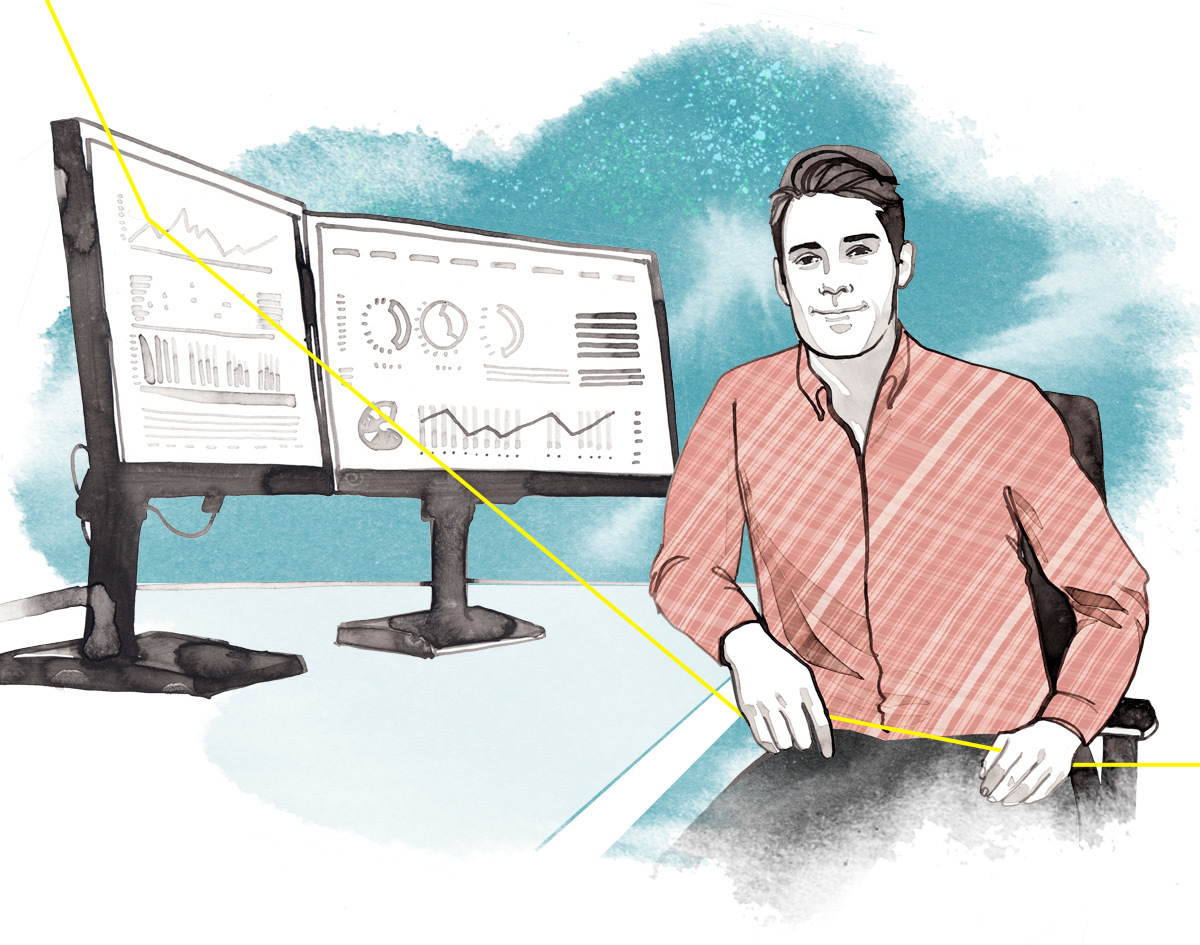
请不要管道。我们选择主题并解决它们。
Once a project to tackle has been identified, a suitable digitalisation strategy must be selected. “We are not interested in commissioning large, tailored programming projects which then simply do not work,” says Räntzsch. “We use fairly standard solutions which already work and simplify processes using software where we can.” The foundation for all of this is high-performance, failure-resistant Wi-Fi and the right in-house network – so expanding our digital infrastructure was the first pillar of the project. Then we turned to the core issues of production control, automation and intralogistics. An MES system is at the heart of our production software, and it will be expanded incrementally with SAP interfaces by 2021. “We used to use Excel a lot, as manysites do,” acknowledges Räntzsch. “That works, but it is labour-intensive and relies on just a few experts.” The new system is even able to handle all of the detailed production planning, from preproduction to final assembly and all the way to quality control. “At the moment, we are finding potential for optimisation on an almost daily basis,” says Räntzsch. “For example, our injection moulding machines have always had high capacity utilisation, but the MES has managed to improve this.”
Humans and machines: working hand in hand
数字革命已经达到世界的工作,and some companies are automating with the goal of reducing staffing levels. Katja Räntzsch explains why that is not the goal in Bühlertal: “At the core of all of this is the goal of increasing the plant’s output – by improving working conditions and smoothing processes." So the production lines were analysed, showing where work could be made easier. The final assembly of the K2 pressure washer involves manually installing the 2 kg pump – a very strenuous and not particularly ergonomic task when repeated over and over. From 2020, this task will be completed by a machine. Steps will also be taken to ease the strain of working on our professional products. This will be particularly advantageous when dealing with the heavy machines. “Just like in the automotive industry, underride driverless transport systems will take the HDS high-pressure cleaner to each workstation in future – greatly improving ergonomic standards.” Once a product is ready to be picked up, the packaging robot places it on a pallet. The machines are then picked up by a driverless transport system (DTS). “This is truly fascinating technology,” reports Räntzsch. “And the DTSs work using swarm intelligence. They don’t simply complete a route; the DTS closest to the current task will pick the product up.” Then it goes to the warehouse or to direct dispatch – where the plant has improved its quota from 30 % to 50 % using the measures already implemented, with a goal of 70 % going forward. “Direct dispatch means orders are addressed and sent out quickly, with minimal storage costs.”
Well on the way – but not there yet: progress is motivation
许多举措已经或处于在Bühlertal实施的过程中 - 这就是两年内。“我们也在成为一家造林的途径,”Räntzsch报道“。在与整个公司的换算策略中保持一致,我们正在在工厂设置人力资源管理,以便没有自己的计算机的员工可以使用数字终端设备要求假期并报告病假。由于所有这一切的证据,增加了生产力和成本的降低是所有这一切的工作。“但是这个项目不是我们的结束;这只是一个开始,“Räntzsch笑着说。“因为我们每天都想进一步走一步,就像我们到目前为止一直在这样做 - 总是可以完成更多。”
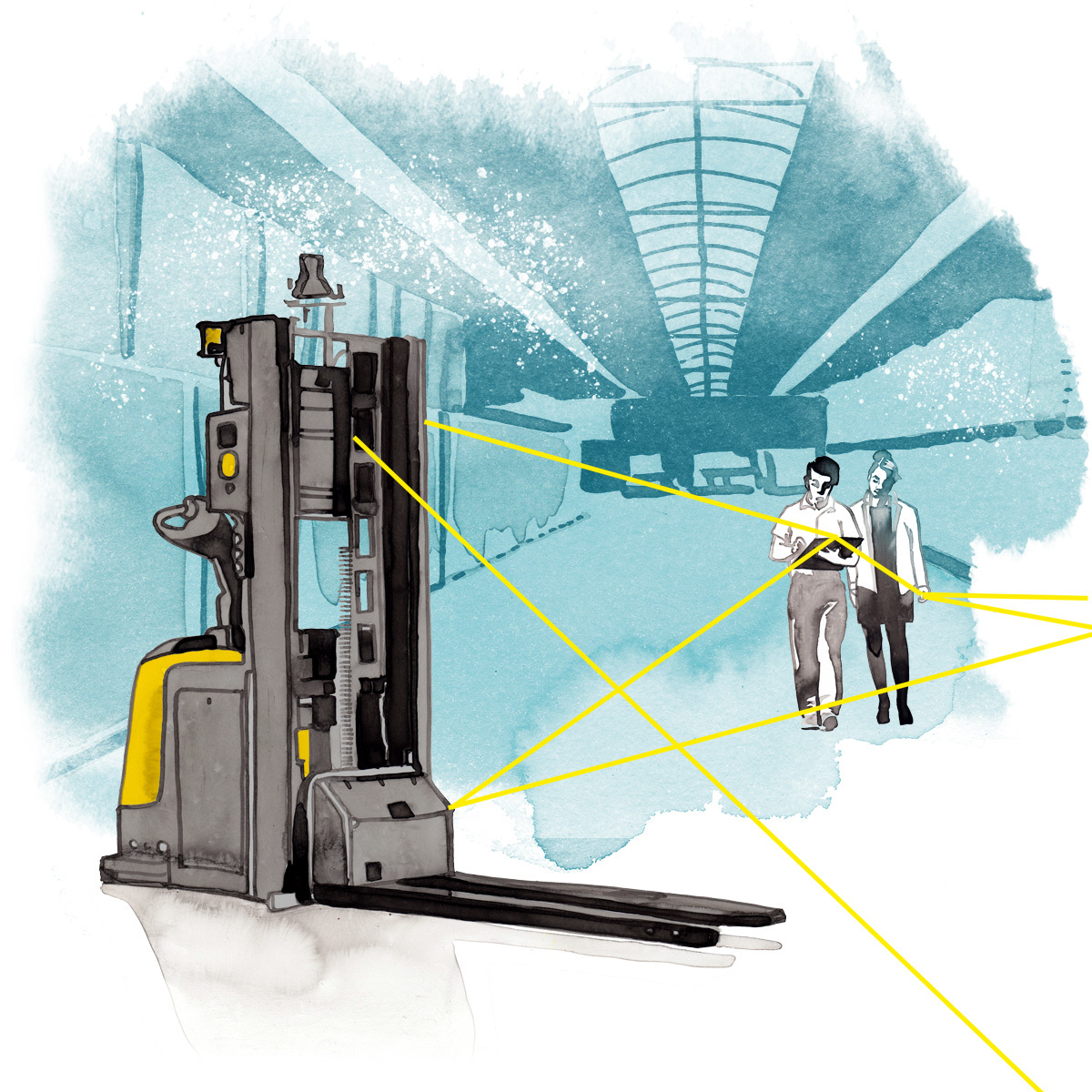
事实与数据Bühlertal 5.0
In demand at Jungheinrich: INTRALOGISTICS TO COMBAT WASTE *
Jungheinrich specialise in intralogistics solutions, and they provided support for Kärcher with the Bühlertal 5.0 project. What are the biggest challenges today?
Markus Staringer:出于一开始,我们很少在空白板岩上实施我们的解决方案。我们通常根据现有流程和装配工作流程工作。我们与客户合作,调查资源在不必要的旅程,等待时间和储存等事物上浪费资源。然后我们优化使用此过程的基础。对系统可用性的需求非常高。为了确保可用性,我们有大约8,000名客户服务技术人员值班,以便我们可以在最短的时间内弥补任何问题。
流程越来越重叠,主要是桥接储层学和生产。您在哪里看到更有效率的最大潜力?
Markus Staringer:That only becomes clear when you look at the process chains. At Kärcher, for example, the merchandise leaves the injection moulding machine, then the injection moulded parts go to production and finally the products go to the warehouse or to dispatch. If these steps run automatically, the risk of error is significantly reduced and work can continue uninterrupted, with reliable cycle times. All of that means that investments in intralogistics pay for themselves quickly.
Digitisation, automation and artificial intelligence – the magic three. Much is already possible, but what will the future hold?
Hennes Fischbach:There has been a constant trend towards automation in intralogistics for decades now. Current solutions are incredibly reliable and our customers really value that. You see, the mantra is: the production environment is far too sensitive for experiments. Artificial intelligence is a buzzword tied up with all kinds of visions and dreams these days. What AI really means is that machines are able to learn and, within a specific framework, independently find the right solution. It also means that we as humans are delegating more responsibility to machines. It will be some time before we are really ready for that and sure that it is safe.
* Markus Staringer和Hennes Fischbach是JungheinRich的项目经理,并监督Bühlertal5.0项目。
You may also be interested in:
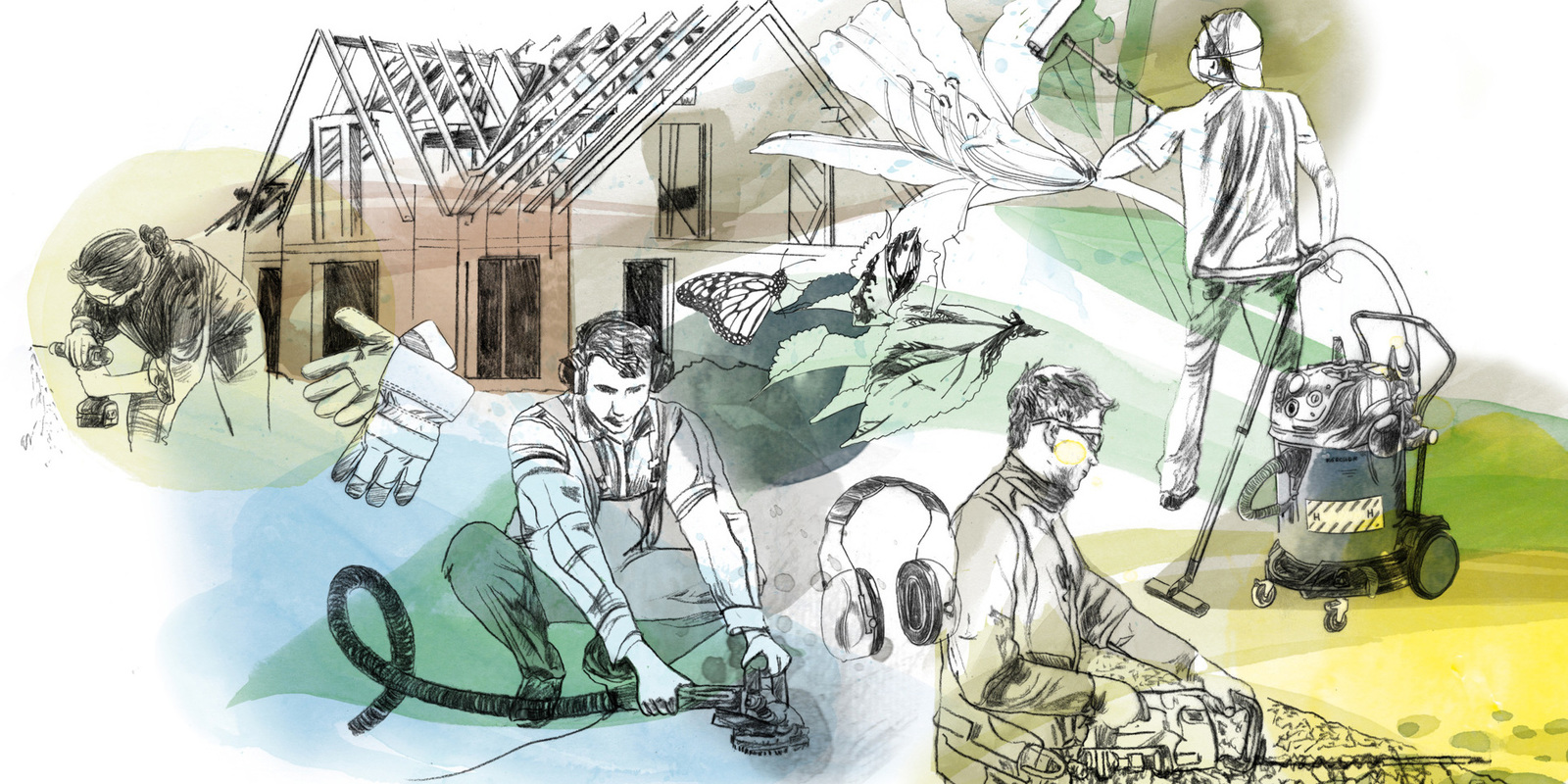
Two worlds, one goal: perfection
Kärcher at home on the patio. Kärcher in building cleaning. People most often think of these two areas of application when it comes to vacuum cleaners, high-pressure cleaners, etc. But it is hard to imagine everyday life without many Kärcher products, especially for workshops.
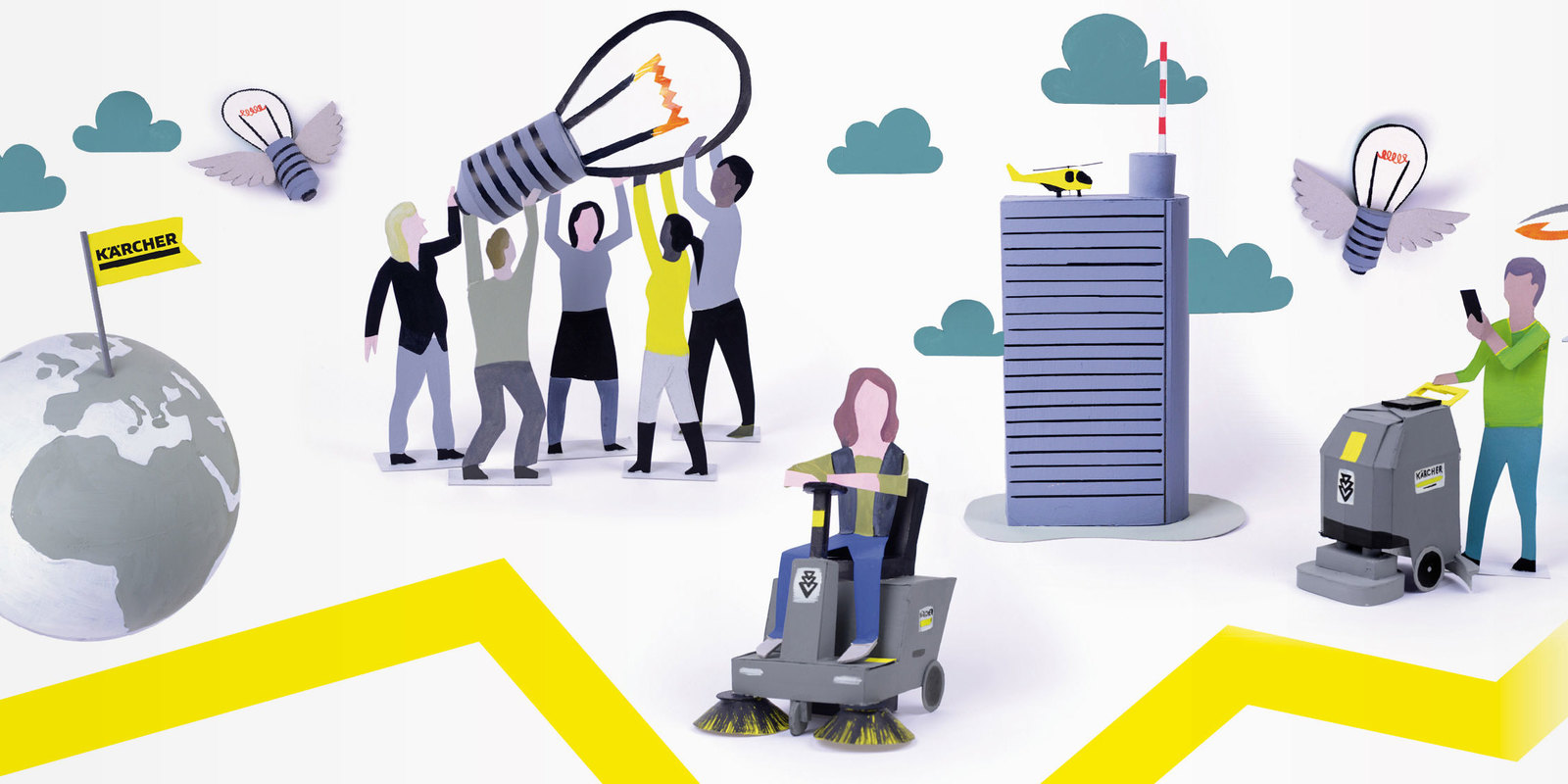
让想法在没有失去触摸的情况下乘飞机
一家公司存在几十年,拥有数千名员工,并在全球各地活跃。另一家公司是全新的,所以说话,由五个信徒组成和一个好主意。这是一个已知的事实,这两个世界可以非常妥协地工作并创造创新。它也是关于桥接主要差异。
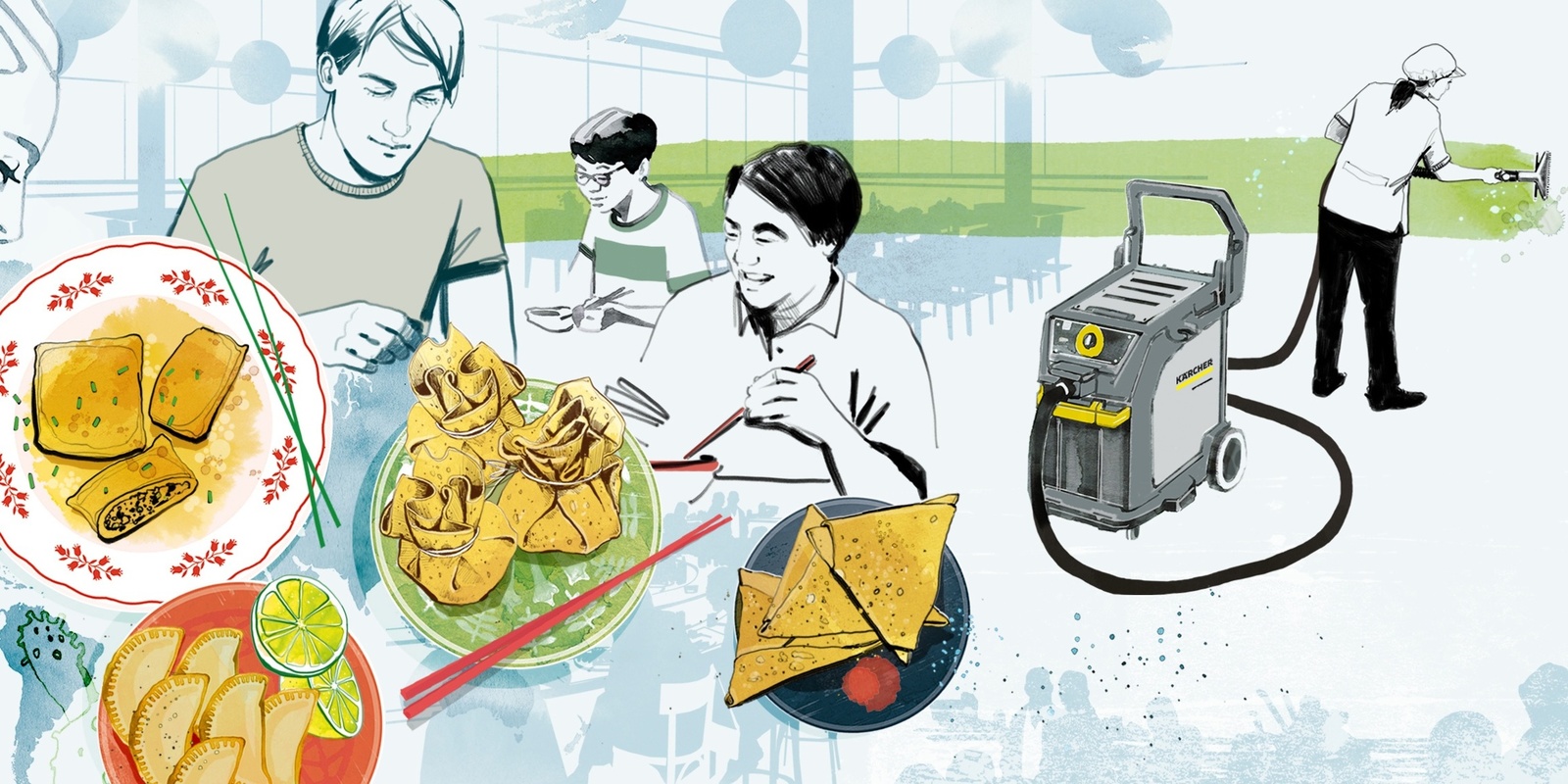
On the track of a swabian speciality
Maultasche(斯瓦比亚馄饨)和kärcher有一件事:他们都来自斯瓦比亚,可以在世界各地找到。像Kärcher产品一样,这些美食包裹在面团中遍布全球。加入我们的简短旅程,展示了烹饪美食如何将人们带到一起以及清洁技术如何确保无忧无虑的盛宴。